Dry Ice Blasting Applications:
Dry Ice Blasting Systems for Coffee Roasters
Clean coffee roasting and packaging equipment in significantly less time, while ensuring safe cleaning with food-grade dry ice blasting.
Coffee roasters, grinders, and packaging equipment become clogged with burnt-on coffee grounds.
Cleaning coffee roasters by manually scraping with hand tools is time-consuming and labor-intensive. Hand cleaning typically takes eight to ten hours to clean one roaster. This method may also include adding water, which leads to the potential for bacterial growth and extended drying time.
Dry ice blasting systems for coffee roasters and packaging equipment is considerably less time-consuming, without creating secondary waste or adding water. Using dry ice blasting, a roaster can be cleaned in just two hours.
It also safely cleans food-grade surfaces, does not add foreign material or allergens, and reduces the risk for microbial growth and cross-contamination.
SPECIFIC USE CASES
Dry ice blasting safely cleans coffee roasting and packaging equipment in both traditional and K-Cup coffee bean roasting facilities.
- Coffee roasters
- K-Cup production lines
- Grinding pots
- Mixers
- Glue applicators
- Labelers
- Wrappers
- Conveyors
- Baggers
- +More
RELATED INDUSTRIES
Benefits of Dry Ice Blasting
Quickly and effectively clean all equipment on coffee roasting and packaging lines.
Increase production uptime, while reducing risk of microbial growth, introduction of allergens, and cross-contamination.
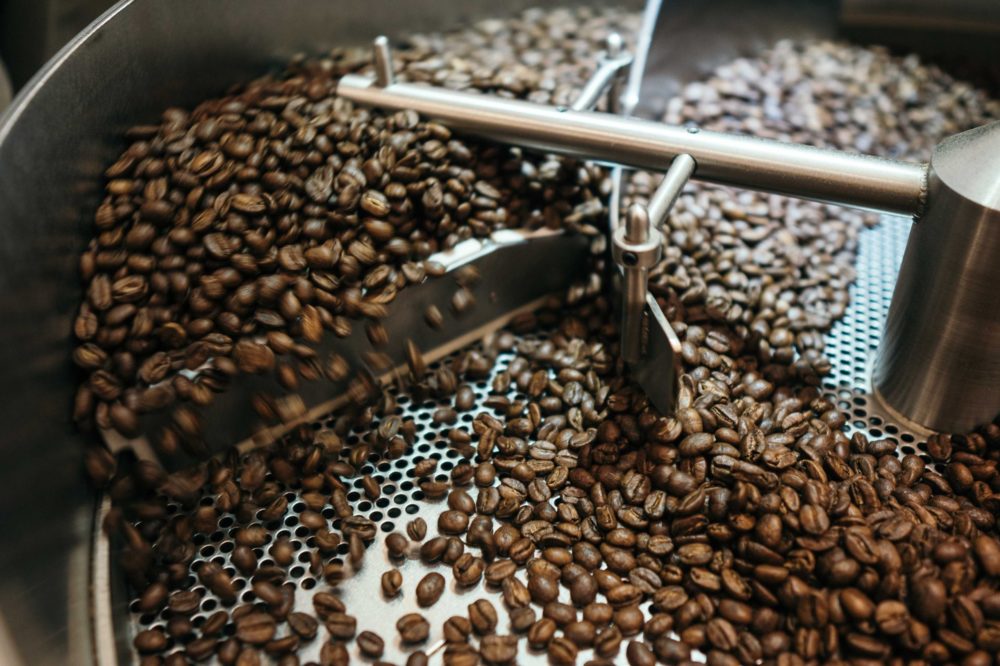
- Significant time savingsReduce cleaning time from 8-10 hours to 2 hours
- No secondary wasteNo introduction of foreign material or allergens
- Safe food-grade cleaningEliminating water reduces risk of microbial growth
- Eliminate cross contaminationFully remove grounds from one blend before roasting another blend
- Environmentally SustainableSignificantly reduce water use in your sanitation process
- Increase production efficiencyCleaning more regularly leads to increase production time
- Non-abrasiveNo risk of damaging equipment
- Clean in-placeMinimal disassembly needed
WE ARE HERE TO HELP.
Interested but don’t know where to start?
Contact us today to learn more about our solutions and see how they can meet your unique needs.