We saw an immediate effect on our CO2 ratio from 2.4:1 now to 1.35:1. Profit, production capability, and overall company performance is greatly improved.
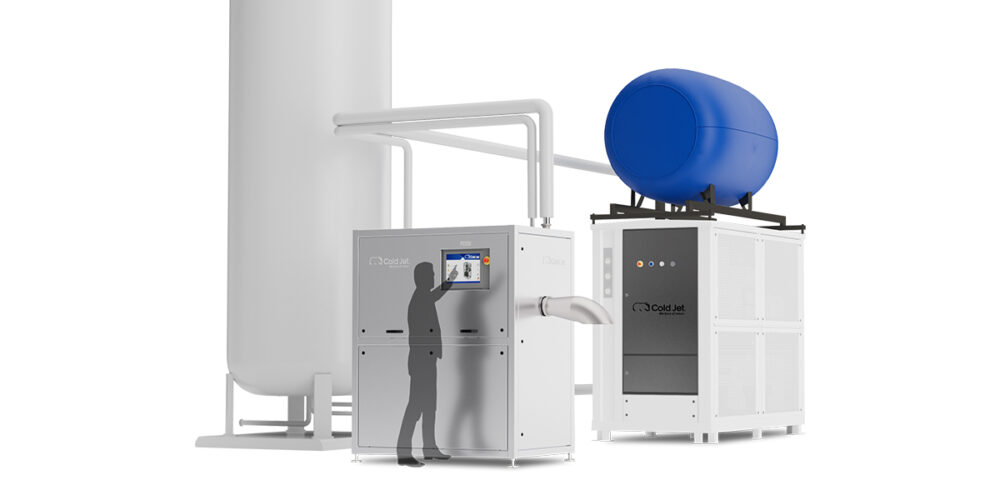
RE-CO2 RECOVERY SYSTEMS
Cut your liquid CO2 costs in half with our RE-CO2 Recovery Systems
DRASTICALLY IMPROVE CONVERSION OF
LCO2-TO-DRY ICE
Reduce your dry ice production costs by up to 40% by recycling exhaust CO2 gas back into your dry ice pelletizer to produce dry ice!
Dry ice production uses liquid CO2 (LCO2), which when brought to normal atmospheric pressure in a pelletizer chamber, half of this liquid is converted to CO2 snow, and the other half is converted to gas. The CO2 snow is then compressed into dry ice pellets while the gas is typically vented into the atmosphere.
By using our RE-CO2 Recovery Systems, the revert gas is collected and recycled to make more dry ice pellets. With a modular design and multiple liquefaction capacities, we ensure that you will drastically improve the conversion rate of LCO2-to-dry ice.
Our RE-CO2 Recovery Systems integrate easily with all Cold Jet (and many competitor) dry ice production systems, including our Integrated Blasting Systems!
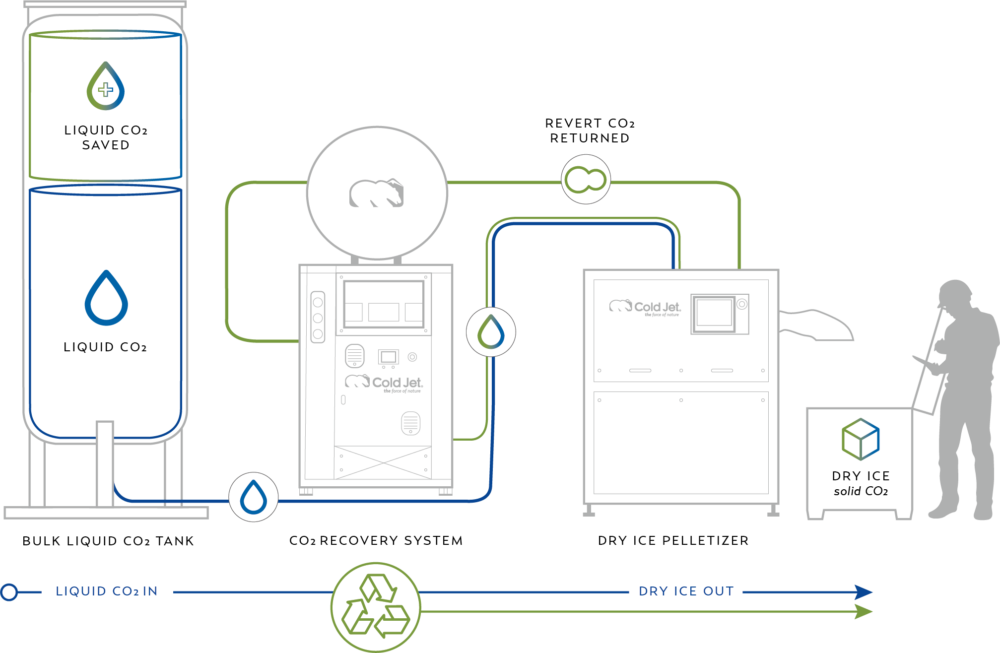
How does it work?
The CO2 Recovery Systems capture exhaust CO2 gas from the vent of a dry ice pelletizer and circulates it back into the pelletizer. Within the recovery unit, the gaseous CO2 is cooled and compressed to create liquid CO2 that is then piped right back to the dry ice pelletizer.
This process reduces LCO2 consumption by almost half in most installations!
Greater Sustainability.
Reduce carbon footprint. Increase dry ice output.
Customers utilizing our RE-CO2 Recovery Systems have experienced production increases of up to 70% more dry ice while utilizing the same amount of LCO2.
This process recycles an already recycled product and greatly reduces the amount of exhaust CO2 that is vented into the atmosphere from typical dry ice production.
Greater Versatility.
Modular design. Countless configurations.
Our RE-CO2 Recovery Systems offer dry ice production facilities the ability to configure a recovery system according to their needs. Offering a modular design, and three different liquefaction capacities, our experts will work with you to ensure your recovery unit will be the perfect fit to significantly improve your LCO2-to-dry ice conversion ratio.
Because of its modularity and ease of integration, you can start small and continuously enhance your processes as efficiency and profit margins increase.
Customers already increasing profits, performance, and production output.
Greater Integration.
Recover CO2 from nearly any dry ice pelletizer brand.
Our RE-CO2 Recovery Systems can be easily integrated into your current dry ice production process and are compatible with almost every pelletizer brand on the market. If floor space is limited, they can be installed outside near a bulk LCO2 tank. We will help you with the electrical needs.

What CO2 Recovery System is best for you?
-
The RE-CO2 320V2
Ideal for pairing with PR350H and PR750H dry ice pelletizers, the RE-CO2 320V2 is the most intelligent, scalable, and sustainable CO2 recovery system of its size available.
-
The RE-CO2 160
Ideal for pairing with PR120H dry ice pelletizers.
-
The RE-CO2 80
Ideal for pairing with PE 80 dry ice pelletizers.
Start doubling your dry ice output today!
CO2 Recovery Frequently Asked Questions
WE ARE HERE TO HELP.
Interested but don’t know where to start?
Contact us today to learn more about our solutions and see how they can meet your unique needs.