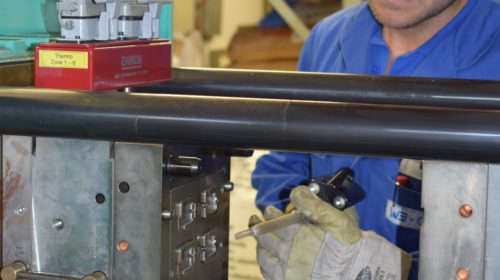
Plastics processor reduces cleaning time from 4 hours to less than 10 minutes
THE SITUATION
In the production process of injection molded parts, the tool cleaning is a crucial but unproductive step. Marquardt solved this issue with an innovative dry ice cleaning system. The system reduces cleaning time and machine downtime by 95% while improving process security.
In every vehicle from well-known automotive suppliers you can find mechatronic or electromechanical Marquardt GmbH parts. A Rietheim based, independent, family company, Marquardt GmbH is the international leader in supplying driving systems and control panels. In addition to vehicles, you can find Marquardt products in control and operating panels in household equipment and other industries. Marquardt is also the world leader in electric tool switches. The company employs 6,000 employees in 12 locations and nine countries. Annually, Marquardt invests 10% of its turnover into research and development.
THE PROBLEM
Modern development tools, simultaneous engineering and effective experimentation are equally important in high-modern injection molding. With 100 machines, the company produces around 3,000 different products. There was one step in the work process that was still done manually: the cleaning of the injection molds.
“Clean tools are a must for the product quality,” explains Dieter Stais, product manager of Marquardt for Riethem-Weilheim. “Contaminants cause damaged parts and waste. Therefore we clean in fixed cycles.”
For manual cleaning, the tools needed to be removed, installed and aligned again. That’s why they had a production downtime of four hours. In addition, the cleaning was not guaranteed, reliable and became staff related. It could also not be excluded, as the mechanical cleaning could lead to damage or increased wear on the tools. This process needed to be optimized.
THE SOLUTION
The solution was the innovative dry ice cleaning system: The Cold Jet i3 MicroClean®-S4.
”The theme of dry ice cleaning was actually already closed,” said Dieter Stais. “The reason for that was a Cold Jet competitor came by with his equipment and asked us to try it. Dry ice cleaning with pellets didn’t function and the machines couldn’t be adjusted to our needs. With Cold Jet, the representative did some testing on the injection molds and adjusted the system to our needs.”
To make sure the system was the best solution, Marquardt tested the equipment for four weeks.
With the MicroClean system, the carbon dioxide comes in the form of ice blocks. The blocks are made of carbon dioxide which is captured as a by-product in chemical or industrial processes. It is reclaimed CO2 and does not contribute to the greenhouse effect. This by-product is created with, for example, the brewing of beer, and can be ordered as a standard industrial gas over the corresponding trade. For cleaning, microparticles are scraped of the dry ice block with the patented shaved ice technology. These particles have, in comparison to pellets, a more refined blasting swath, allowing a more smooth and effective treatment. At the same time, the i3 MicroClean-S4 operates much quieter.
“With this dry ice cleaning technique, we can clean our injection molds hot in the press and without disassembly,” reported the production manager.
This is possible, on one hand, as blast pressure and ice volume are adjustable. On the other hand, there are different high performance nozzles. For the cleaning of wide areas a nozzle with a blast swath of 2.2 cm would be appropriate. The low flow round nozzle guarantees a punctual and reliable removal of persistent dirt. The cleaning of difficult-to-reach areas and undercuts are done with a 90° angled nozzle. In addition, a rotary union allows the nozzle to turn 360° and to reach all areas. During the work, the ergonomically designed applicator with integrated LED-light gives optimal illumination for the areas that need to be cleaned.
THE RESULTS
To clean, the mobile and compact device can be easily moved to the injection molds and then connected to the compressed air supply and the static cable.
“The machine gets adjusted and the cleaning work gets done within five to ten minutes,” said Dieter Stais. “Compared to the four hours we had before, the productivity is increased significantly.”
The i3 MicroClean reduces cleaning time up to 95%; therefore, it paid for itself within a very short time. This is an aspect the people at Marquardt were very pleased with. Another aspect is the optimized process reliability.
“Unlike manual cleaning, we can certainly remove contaminants with dry ice cleaning,” said the production manager. “This also results in a contribution to the overall optimization of our production process.”