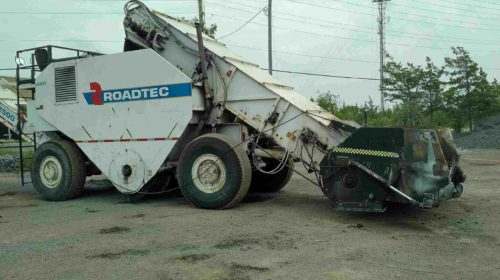
Dry ice blasting reduces cleaning time of asphalt truck from one week to one day
THE SITUATION
Prime, Tack & Seal Company (PTS) in West Chicago, Illinois, specializes in spraying prime and tack coats, as well as applications for dust control, chip and seal and aggregate slope paving on a large variety of road projects. PTS applies an asphalt mixture to existing asphalt or concrete surfaces and to new construction sites prior to asphalt paving. This mixture helps prep the surface before the top layer of asphalt is applied by plugging voids in the surface, hardening the top layer and helping to bind it to the overlying asphalt. The trucks that carry and spray the asphalt mixtures are called prime trucks and accumulate layers of hardened asphalt, rocks, sand and other materials over time. This build-up on the spray bars and nozzles can result in clogging and also makes the trucks more difficult to maintain.
THE PROBLEM
Traditionally, PTS cleaned the trucks on a bi-annual basis with various chemicals and pressure washing to remove the layers of build-up. However, this process was repetitive, time consuming and did not fully clean the trucks. They would spray the chemicals on the build-up, let it sit for awhile and then blast it with a power washer. They would have to do this process several times until the build-up could be removed, taking up to a week or more to clean one truck. The company also had to spend the time and resources on collecting and disposing of the leftover water because it had to be treated as a hazardous waste. The process could also result in employee exposure to the chemicals.
THE SOLUTION
PTS was searching for a more efficient process to clean their trucks. National Industrial Maintenance, a specialized maintenance contractor, contacted PTS. Howie Wirkus, Project Manager at National Industrial, introduced them to Cold Jet’s dry ice cleaning process and PTS was impressed with the results during a demonstration and decided to contract National Industrial to dry ice blast clean their trucks.
Cold Jet dry ice cleaning uses non-abrasive media in the form of recycled CO2 pellets that clean without damaging surfaces or equipment. The combination of dry ice cleaning’s kinetic energy and thermal effect breaks the connection between the dirt and surface, lifting away contaminants. Unlike blasting with other media, dry ice cleaning does not leave any secondary waste, because the dry ice particles sublimate upon impact – converting from solid to gas. Dry ice cleaning is safe and non-toxic, does not create downstream contamination and reduces or eliminates employee exposure to dangerous chemical cleaning agents. Dry Ice blasting cools the asphalt on contact, making it easier to remove, leaving the original substrate undamaged.
THE RESULTS
Dry ice cleaning has proven to be a much more effective cleaning process and produces better results in a fraction of the time.
“It’s at least twice as fast, if not faster,” said Wirkus. “With dry ice cleaning, as soon as you hit the build-up, it flies off.”
Using the Cold Jet Aero 80FP system, National Industrial is able to fully clean one truck per day. It previously took PTS one week to clean one truck. They clean 13 trucks total for PTS on a bi-annual basis. National Industrial uses about 1.5 dry ice totes per truck, which is about 750 pounds of dry ice.
“During the summer months, we’ll just clean the back of the trucks, which includes the nozzles and tank, and during the winter when PTS is doing their annual maintenance, we will clean the entire truck,” said Wirkus.
Dry ice cleaning not only makes the trucks easier to maintain, but it also makes them more efficient.
“The drivers of the trucks love it because it’s much cleaner and they have less problems, such as the nozzles clogging,” said Wirkus.
PTS was so impressed with dry ice cleaning that they are considering using it to clean other assets and machinery, such as their holding tanks and hoses.
“They love it because it’s cost effective, the clean-up is so much easier, it’s safer and it’s environmentally friendly,” said Wirkus.