Dry ice cleaning results in a superior clean. And, with less downtime, we have been able to increase production. Our customers have very stringent quality control procedures and demands, and dry ice cleaning has helped us meet those requirements. The detail of cleaning we get with Cold Jet’s system allows us to clean areas that otherwise could not be cleaned.
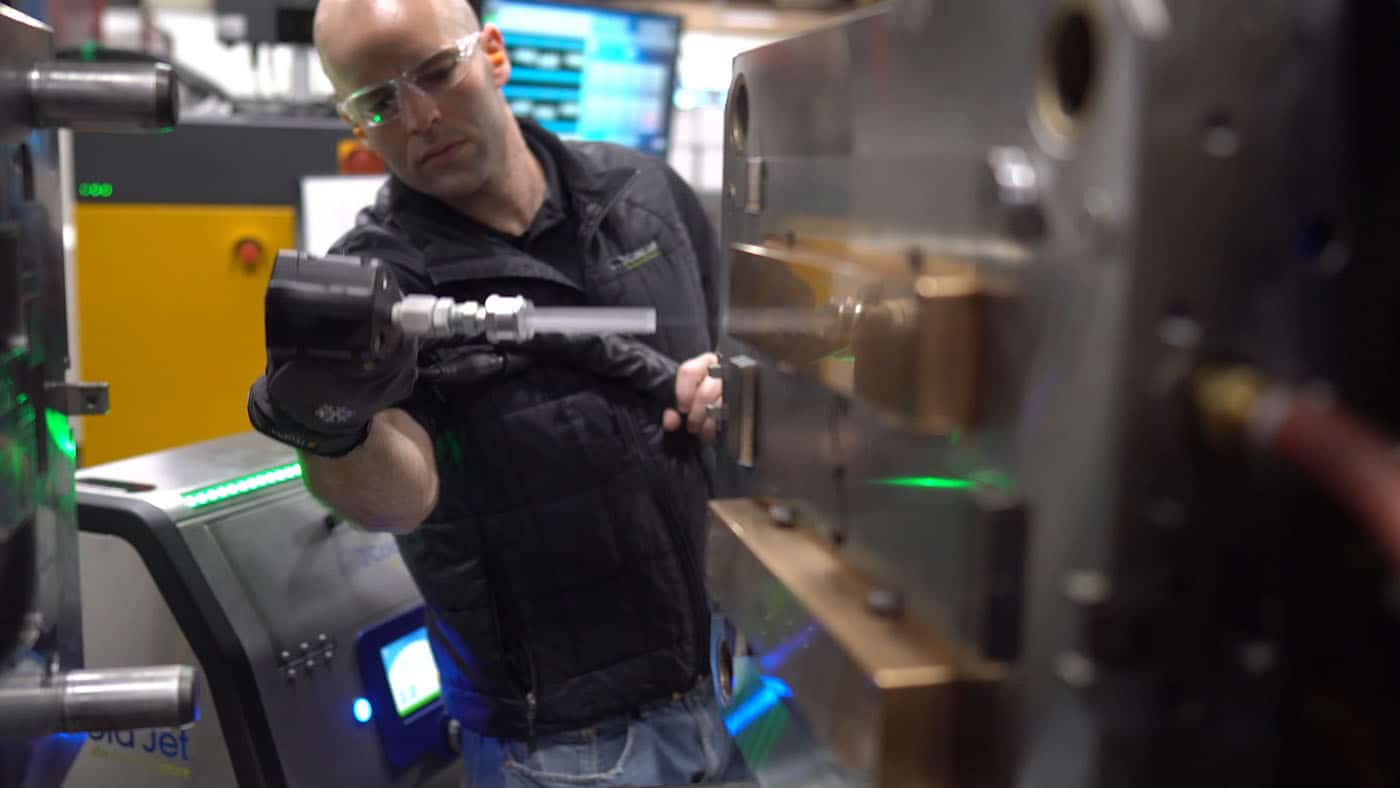
Dry Ice Blasting Machines for Medical Equipment Manufacturing
Clean Medical Molding and Safely Deburr High Tolerance Medical Parts with Dry Ice Cleaning
Dry ice cleaning is an effective, safe, and consistent cleaning process that results in high quality end products
Medical equipment manufacturers of high tolerance medical parts require the highest standards of quality, product consistency, and safety. Effectively cleaning microcavities on precision medical molds is critical to consistently producing high quality medical parts. Similarly, removing parting line flash (deflashing) or material burrs (deburring) from final products is critical for quality, patient safety, regulatory compliance, and device longevity.
Dry ice blasting for medical mold cleaning and medical deburring is non-abrasive and will not damage molds, tooling, or components. The medical parts cleaning process does not produce secondary waste, and provides a more effective and consistent clean.
Contact us today to discover how our dry ice cleaning machines can enhance your medical molding, medical deburring, or medical device parts cleaning processes.
What are the Benefits of Dry Ice Blasting in Medical Equipment Manufacturing?
Dry ice blasting is non-abrasive and enables safe and consistent cleaning
Traditional cleaning methods for medical molding are often slow, labor intensive, and potentially damaging to the molds. The process of deburring or deflashing medical parts presents similar challenges, especially for delicate parts with complex geometries. Traditional medical deburring methods are slow, risk damaging the part, and can leave media lodged in part features.
Dry ice cleaning is non-abrasive and preserves mold surfaces and product integrity. It’s a more efficient process for removing contaminants from medical molds and burrs from medical parts. The medical part cleaning process improves product consistency and quality while reducing scrap rates and rejections. Dry ice sublimates upon contact, leaving no residual media, chemicals, or other contaminants on the finished parts.
-
Non-Abrasive Cleaning Process
Dry ice blasting is a non-abrasive cleaning process that preserves the integrity of medical molds, medical equipment, and final products. The cleaning process preserves the surface finish of molds and does not alter features like letters, numbers, or trademarks on the mold. In deburring and deflashing processes, dry ice blasters will not affect the geometry or surface finish of parts.
-
Faster and More Effective Clean
Dry ice blasting equipment delivers superior efficiency for cleaning precision molds and deburring or deflashing high tolerance medical parts, significantly reducing cleaning time. The process effectively cleans molds and removes burrs, flash, and contaminants leftover from the manufacturing process. It eliminates manual cleaning methods, and provides a cleaner alternative, streamlining operations for optimal productivity.
-
Maintain Product Consistency and Quality
Dry ice blast cleaning maintains product consistency and quality by helping healthcare equipment manufacturers meet contract specifications while improving overall product consistency. Cleaner molds produce higher quality products and reduce scrap rates.
-
No Secondary Waste
Dry ice sublimates and leaves no waste. HEPA filters capture removed contaminants. Companies have tested, validated, and use dry ice blasting in ISO 8 – Class 100,000 clean rooms.
-
No Residue or Additional Contaminants
Dry ice sublimates back to gas, leaving no chemical residue or other contaminants on finished parts.
What Can Dry Ice Blasting Clean in Medical Equipment Manufacturing?
Dry ice blast cleaning for medical manufacturing helps meet industry standards. The process is an effective cleaning solution for durable medical goods, disposable medical goods, and implantable medical goods.
-
Class I Devices
-
Class II Devices
-
Class III Devices
-
ISO 8 – Class 100,000 Clean Rooms
-
ISO 7 – Class 10,000 Clean Rooms
Safely Clean Medical Molds Online While Preserving Critical Mold Details with Dry Ice Cleaning
Dry ice blasting enables plastic and rubber molds to be consistently and reliably cleaned. This ensures medical parts and components remain within specified tolerances.
-
Clean molds in-press
Dry ice cleaning machines clean medical molds while they remain hot and online – including in ISO 8 (Class 100,000) and ISO 7 (Class 10,000) clean rooms. This eliminates downtime associated with the cooldown, disassembly, and reassembly processes. Molds can be cleaned more frequently, which significantly decreases rejection rates and increases production output.
-
Preserves mold surface integrity
Dry ice blasting is safe and effective on Class A through D surfaces. The medical mold cleaning process is non-abrasive and will not damage mold finishes or critical mold details. Details like the measurement indicators on syringes, are accurately reproduced in every production cycle. Dry ice cleaning significantly reduces high tooling replacement costs and prolongs the lifespan of valuable molds.
-
No residue or secondary waste
Dry ice cleaning leaves no solvent residue or secondary waste on molds. This eliminates additional cleaning needs, reduces scrap, and ensures high-quality end products.
-
Removing residue from medical molding with dry ice cleaning
-
Dry ice blaster removing TPE from medical molding
-
Cleaning medical molding in the press with dry ice blasting
-
Class A-D Surface Mold Cleaning
-
Injection Mold
-
Compression Molds
-
Rotational Molding
-
Thermoform Molds
-
Dip Molding
-
Blow Molding
-
Extrusion Dies
-
Rubber Molds
-
Micro Molds
Dry Ice Cleaning Deburrs and Deflashes Medical Parts Without Impacting Surface Finish or Part Geometries
Dry ice blasting is a non-abrasive and precise deburring and deflashing solution for medical components.
-
Protects part finish and geometries
Dry ice blast cleaning preserves surface finish, part geometry, and tight tolerances while delivering consistent, repeatable results. The medical deburring and deflashing process is reliable and cost-effective for low-volume, high-value parts.
-
Precise and targeted part finishing
Dry ice cleaning enables precise and targeted deburring on specific part areas. It can access complex geometries and intricate internal channels while maintaining precise control over cleaning parameters.
-
No media entrapment
Dry ice turns directly from solid to gas upon impact. This eliminates the risks of residual media, cross-contamination, and media becoming lodged in small features or holes in the part.
-
Deburring orthopedic implant using dry ice blasting
-
Deburring medical device component with dry ice cleaning
-
3D printed medical implant deburring with dry ice blasting
Dry ice blasting machines can deburr and deflash small complex parts, such as: implants, stents, surgical tools and instruments, micro-tools, catheter tips, manifolds, Delrin gears, and cannulas. The medical deburring process is also effective on larger parts that cannot fit in traditional deburring machines. The process is effective on a variety of materials, including:
-
PBT (Polybutylene Terephthalate)
-
Acetal
-
Nylon
-
LCP (Liquid Crystal Polymer)
-
ABS (Acrylonitrile Butadiene Styrene)
-
PP (Polypropylene)
-
PEEK (Polyether Ether Ketone)
-
Titanium
-
Stainless Steel
-
Nitinol
-
Additively Manufactured Components / 3D Printed Parts
What Do Medical Equipment Manufacturers Need for Dry Ice Cleaning?
A complete dry ice blasting system requires essential supporting equipment beyond the dry ice blaster. When implementing dry ice cleaning in your facility, the following components are essential for an effective setup:
-
Dry Ice Blaster
The foundation of your medical parts cleaning and medical deburring program starts with a reliable and easy to use dry ice blasting system. Cold Jet offers a variety of machines to choose from, including models with features like the patented Particle Control System (PCS®). The PCS enables you to fine-tune blasting parameters and particle size to adjust cleaning power from very gentle to more aggressive. The systems will come complete with a blast and air hose, an applicator, and a nozzle that is best suited for your application.
-
Air Compressor
Compressed air can be supplied from your facility’s existing filtered air system. For medical equipment manufacturers, clean and dry air is critical. Systems should include moisture separation and oil filtration to prevent contamination. Typical dry ice cleaning systems require 100 cfm (2.8 m³/min) at 80 psi (5.5 bar). The Cold Jet PCS Ultra comes with an additional water separator attachment if needed.
-
Medical Dry Ice Supply
Regular access to high quality dry ice is essential for maintaining continuous cleaning operations. Average consumption is approximately 88 lbs. per hour. Partner with suppliers who can certify their dry ice meets industry standards. Establish a delivery schedule aligned with your medical device parts cleaning and parts finishing schedules.
-
Machine and Operator Training
Operators need proper training to use dry ice blasting effectively for cleaning medical instruments, medical mold cleaning, and medical deburring. Cold Jet offers a training course that teaches your team how to use the machine safely and correctly. The course covers essential operating techniques for contamination-free cleaning, effective cleaning practices, and safety guidelines.
-
Personal Protective Equipment (PPE)
Medical parts cleaning staff should wear proper safety gear, including gloves, hearing protection, and eye protection. In clean rooms, they should also wear appropriate gowns, hair covers, and shoe covers.
-
Automated Cleaning System (Optional)
Medical deburring processes using dry ice blasting are commonly automated. Fully automated dry ice cleaning systems combine a dry ice maker, dry ice blaster, robotic arm, and blast cabinet in one system.
What Is the Best Dry Ice Blasting Machine for Medical Equipment Manufacturing?
Cold Jet offers a comprehensive range of dry ice blasting machines for medical device manufacturing environments. Our user-friendly machines are ideal for medical components precision cleaning and medical mold cleaning. Our Particle Control System cleans your tools and products safely while helping you work more efficiently and meet strict medical regulations and clean room standards.
-
Aero2 PCS ULTRA
The Aero2 PCS ULTRA is a versatile machine for a variety of medical molding and medical deburring applications, from extremely gentle cleaning with MicroParticle dry ice to aggressive cleaning of larger surfaces with 3 mm dry ice granules.
Aero2 PCS® ULTRA -
i3 MicroClean 2
The i³ MicroClean 2 is the next generation of precision cleaning. It offers better efficiency and intuitive controls in a lightweight and compact system. Easily control cleaning aggression to lock in the ideal parameters for your specific medical molding or parts finishing application.
i3 MicroClean® 2 -
i3 MicroClean
The i3 MicroClean is an efficient, lightweight machine that is effective in medical mold cleaning and medical deburring and deflashing applications.
i3 MicroClean®
Why Invest in Cold Jet Machines for Cleaning in Medical Equipment Manufacturing?
If you’re upgrading your medical components precision cleaning or precision mold cleaning process, investing in a Cold Jet dry ice blaster enhances your operation’s efficiency while meeting clean room standards.
When evaluating this capital investment, consider both the return on investment (ROI) and operational benefits specific to your medical device parts cleaning facility. Cold Jet machines deliver faster ROI and greater value through:
-
Clean Room Validated
Our MicroParticle dry ice technology is tested and validated to be safe in clean room environments.
-
Trusted Medical Supplier
With more than 24,000 machines installed globally and installations in the leading medical manufacturer facilities, we’ve established ourselves as the trusted solution for dry ice blast cleaning for medical manufacturing.
-
Industry Leading Reliability
Our machines are built to last and have significantly longer machine life than competitors.
-
Lower Operating Costs
Our dry ice blasters use significantly less dry ice, compressed air, and electricity than competitor machines. This reduces your daily operational expenses while maintaining the highest quality of clean and safety.
-
Industry Leading Support and Training
Our regional technicians understand the unique requirements in medical technology environments and are always accessible. We deliver both maintenance services and comprehensive equipment operation training.
-
Application Specific Accessories
Our wide range of accessories, including applicators, blast hoses, and application specific nozzles help you to find the best setup for your medical parts cleaning application.
OUR CUSTOMERS & WHAT THEY SAY ABOUT US
Medical Equipment Manufacturing customers around the world rely on Cold Jet
With a global install base of 24,000+ that consists of companies large and small – Cold Jet delivers real value to medical machine manufactures and medical molders.
WE ARE HERE TO HELP.
Interested but don’t know where to start?
Contact us today to learn more about our solutions and see how they can meet your unique needs.