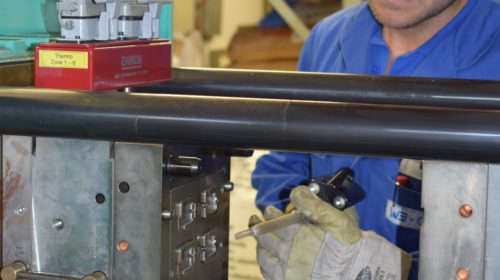
50 % weniger Wartungszyklen durch Trockeneisstrahlen
DIE SITUATION
Durch die heutigen hohen Qualitätsstandards ist die Sauberkeit und somit die Reinigung von Formen ein Hauptanliegen für eine hohe Produktqualität in der Kunststoffindustrie. Eine Spritzgussfirma aus Franken hat die Lösung gefunden.
Die Hans Geiger Spritzgießtechnik GmbH ist eines von drei Unternehmen, die zusammen die Geiger Gruppe bilden. Zusammen mit der Hans Geiger Formenbau GmbH am Hauptstandort ist es im fränkischen Nürnberg angesiedelt. Das dritte Unternehmen, die Reiter HG Geiger Kunststofftechnik GmbH, ist in Hilpoltstein zuhause. Gegründet wurde das Unternehmen 1961 als Formenbau-Betrieb von Hans Geiger. 1968 kam der Bereich Spritzguss hinzu. Damals konzentrierte man sich besonders auf die Sparten Spielzeug und Fotografie, bevor auf Kundenwunsch auch die Kunststofffertigung in Angriff genommen wurde. Heute ist das Unternehmen spezialisiert auf die Herstellung komplexer Bauteile unter wirtschaftlich rentablen Bedingungen und in höchster Qualität. Zu den Kunden des Unternehmens zählen international bekannte Elektronik- und Automobilhersteller.
DIE AUFGABENSTELLUNG
Jedes Erzeugnis ist nur so gut, wie sein Entstehungsprozess. Die Güte und damit letztendlich die Wertschöpfung eines Produkts ist immer das Ergebnis mehrerer, optimal ineinandergreifender Einzelschritte. Nur einer der Gründe, warum im Hause Geiger so viel Wert darauf gelegt wird, den Produktentstehungsprozess ganzheitlich zu betrachten.
„Die Reinigung unserer Werkzeuge ist für unser Endprodukt sehr wichtig. Belagbildung durch die in den Kunststoffen enthaltenen Additive und Flammschutzmittel hat direkten Einfluss auf die Qualität der Produkte und die Lebensdauer der Werkzeuge.“ erklärt Hans Kolb, Prozessingenieur bei Hans Geiger.
Daher sind feste Reinigungszyklen für die Formen festgelegt worden, um sicherzustellen, dass sie gepflegt und in einem einwandfreien Arbeitszustand sind. Bisher wurden die Formen, wenn möglich von Hand in der Maschine gereinigt. Ansonsten musste die Form aus der Maschine ausgebaut und im Formenbau zerlegt werden. Dort wurden die Formteile dann mit Chemikalien, Ultraschallbad, Kirschkernstrahlen oder von Hand gereinigt.
„Wenn Sie eine 96 Kavitätenform von Hand reinigen, ist es nicht nur Zeitaufwendig, es ist auch schwierig hinter jeden Schieber und Winkel zu gelangen.“, sagte Kolb. „Die Reinigung von Hand in der Maschine war nur wenig effektiv.“
Die Reinigung im Formenbau ist zudem sehr zeitaufwändig. Je nach Form wurden bis zu 20 Mannstunden und bis zu 2 Mitarbeiter benötigt. Außerdem bestand immer die Gefahr von Beschädigungen an den Formen. Dadurch wurde die Lebensdauer des Equipments verkürzt und Werkzeugteile mussten gewechselt werden.
Weitere Bedenken gab es durch den neuen Prozessanlauf, Kapazitätsbindung der Mitarbeiter im Bereich Spritzerei, und Formenbau sowie Maschinenstillstandzeiten. Dem Reinigungsprozess mussten je nach Form bis zu 4 Stunden (Ein- und Ausbau der Form) hinzugerechnet werden. Es ist also nicht verwunderlich das Herr Kolb nach einem neuen Reinigungsprozess suchte.
DIE COLD JET LÖSUNG
Durch allgemeine Fachliteratur war er bereits auf das Trockeneisstrahlen aufmerksam geworden. Nachdem er sich bei verschiedenen Anbieter informierte, wurde schnell klar, dass nur ein Blockeisstrahlgerät in Frage kommt. Ein Material-lieferant gab noch zusätzlich die Empfehlung der Firma Cold Jet weiter, welche das i³ MicroClean Trockeneisreinigungssystem mit der Cold Jet patentierten (Block-Shaver) Technologie entwickelt hat.
Die abgeschabten Trockeneis-Mikropartikel werden auf Schallgeschwindigkeit beschleunigt um Verunreinigungen beim Aufprall von der Formoberfläche zu sprengen. Die Kombination der kinetischen Energie und dem thermischen Effekt bricht die Verbindung zwischen der Verunreinigung und der Oberfläche.
Da Trockeneis bei Kontakt sublimiert, gibt es keine Wasserspuren, Waschflüssigkeit oder Trocknung. Cold Jet Systeme beschädigen nicht die Formoberfläche und verändern auch nicht die Abmessungen. Somit ist eine konsistente Produktqualität sicher. Trockeneisstrahlen ist außerdem sicher, ungiftig und verhindert nachhaltige Verschmutzungen und reduziert oder beseitigt die Gefährdung der Mitarbeiter durch gefährliche chemische Reinigungsmittel.
Nach einer Demonstration wurde ein Leihgerät zur Verfügung gestellt und von einem Team aus dem Formenbau getestet. Nach einer Probephase von ca. 4 Wochen wurden die Ergebnisse der Geschäftsführung von Geiger durch das Qualitätswesen vorgestellt. Die gemachten Erfahrungen waren so positiv, dass das
Leihgerät übernommen wurde.
„Diese Reinigungsmethode ist sehr effektiv um den Belag im Werkzeug zu entfernen und hilft teilweise sogar bei auftretenden Verbrennungen.“ berichtet Hans Kolb. „Bei bestimmten Belägen konnten wir die Wartungszyklen bis zur Hälfte erweitern! Dadurch reduzieren sich die Stillstandzeiten und Kosten natürlich erheblich.“
Ein weiterer Gewinn für Hans Geiger ist die Verbesserung der Produktivität, Reduzierung von Risiko und Unterstützung von Umweltinitiativen. Der Kostenpunkt war ein wesentlicher Bestandteil bei der Kaufentscheidung. Kalkulationen für bestimmte Produktgruppen wurden durchgeführt um die reduzierten Aufwände beziffern zu können. Die Firma hat kalkuliert, dass durch die Zeiteinsparung und die Erhöhung der Maschinenauslastung die Investition sich in weniger als einem Jahr amortisiert.
Ein Mitarbeiterteam wurde mit der Überprüfung der Benutzerfreundlichkeit beauftragt. Das mobile MicroClean Tischgerät ermöglicht es den Mitarbeitern das System schnell durch die Produktion zu fahren, um eine Reinigung durchzuführen wann immer und wo immer es nötig ist. Für eine optimale Beleuchtung der zu reinigenden Oberfläche während der Arbeiten, sorgt eine in den ergonomisch gestalteten Applikator integrierte LED-Leuchte. Durch eine 45° und 90° Winkeldüse sowie ein Düsendrehgelenk (ermöglicht 360° Drehung im Werkzeug) ist es jetzt einfach und mühelos schwer zu erreichende Bereiche und hinter Schiebern zu reinigen. Ein weiteres Plus ist, dass sich die Trockeneis- und Druckluftzufuhr individuell regeln lässt und die Einstellungen genau auf die Anforderungen abgestimmt werden können. Für 2 Werkzeuge wird durchschnittlich ein Trockeneisblock benötigt. Das Wartungspersonal hat mehr Ruhe in der vorbeugenden Wartung, da weniger ungeplante Aktionen zur Fehlerbehebung durchgeführt werden müssen. Zusätzlich muss die Form nicht mehr oft zerlegt werden, was zu großer Begeisterung in der Instandhaltung und Spritzerei führt.
Herr Kolb ist Mitglied im Kunststoffnetzwerk Franken. Dort hat er eine Präsentation mit einem Cold Jet Mitarbeiter durchgeführt und das Trockeneisstrahlen vorgestellt, welches zu großem Interesse führte.
„Durch die entscheidenden Vorteile Qualität, Umwelt & Kosten durch Cold Jet Trockeneisstrahlreinigung, findet momentan eine Testphase in unserem Schwesterwerk Fa. Reiter statt, indem hauptsächlich Produkte für die Medizintechnik gefertigt werden.“ merkt der Prozessingenieur abschließend an.