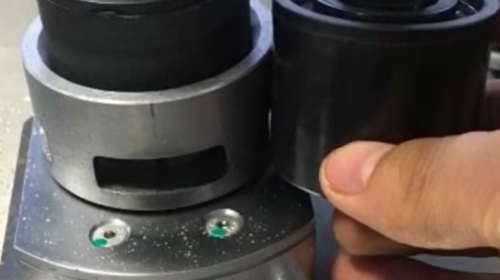
Trockeneisstrahlen für die Spritzgießwerkzeug-Reinigung
DIE SITUATION
In der Reinigung von Spritzgießwerkzeugen steckt viel Potenzial, die Auslastung der Maschinen, die Wirtschaftlichkeit und Prozesssicherheit zu verbessern. A. Raymond, ein international tätiger Automobilzulieferer, erhöhte durch den Einsatz eines innovativen Systems zur Trockeneisreinigung den Maschinennutzungsgrad. Zusätzlich erzielte er dabei eine deutlich höhere Prozesssicherheit.
Geht es um Befestigungselemente, zählt die weltweit tätige A. Raymond Gruppe zu den führenden Entwicklungs- und Produktionspartner der Automobilindustrie. Neben dem Fahrzeugbau beliefert das 1865 in Grenoble gegründete Unternehmen die Branchen Solarindustrie, Haushaltswaren, Luftfahrt, Elektro und Elektronikindustrie sowie die Bauindustrie mit intelligenten Schnellbefestigungs- und Verbindungssystemen aus Metall und Kunststoff. Produziert wird an 20 Standorten rund um den Globus, darunter die bereits 1898 gegründete deutsche Tochtergesellschaft A. Raymond GmbH & Co. KG in Lörrach.
Hier entstehen unter anderem Spezialbefestigungselemente und Schnellkupplungen für die Bereiche Karosserie, Innenausstattung, Antriebsstrang, Klima- und Flüssigkeitsmanagement sowie Fahrzeugelektrik und -elektronik in Spritzgießverfahren. Das sind beispielsweise Steckersysteme, Schraubteile und Scheibenwaschdüsen u.a. aus Polycarbonat, Polyamid und POM, die als so genannte Dauerläufer dreischichtig hergestellt werden.
DIE AUFGABENSTELLUNG
„In den Kunststoffen sind Flammschutzmittel und Additive enthalten, die in den Kavitäten der Werkzeuge einen Belag hinterlassen haben. Dieser muss alle zwei bzw. drei Tage entfernt werden, damit die Qualität der Teile nicht beeinträchtigt wird. Dazu zählt, dass Steckersysteme verschiedene Validierungstests bestehen“, erklärt Stefan Preller, der in der Abteilung Manufacturing Direct Industrialisation (MDI) für die Industrialisierung von Werkzeugen im Kunststoffbereich zuständig ist.
Um die Werkzeuge zu reinigen, wurden sie aus den Maschinen ausgebaut und soweit zerlegt, dass die feinen Kavitäten mit Spezialwerkzeugen, Pinseln und Lösungsmitteln beziehungsweise Formcleanern gereinigt werden konnten. Die Reinigung der Schieber erfolgte in einem Ultraschallbad. Der Zeitbedarf für die Demontage, Reinigung und Montage der Werkzeuge betrug zum Teil mehrere Stunden.
„Die regelmäßigen Reinigungsprozesse haben zu einer signifikanten Reduzierung der Maschinenauslastung geführt. Weiterhin hat der Reinigungsgrad der Werkzeuge direkten Einfluss auf die Teilequalität“, berichtet der Industrialisierer.
Außerdem kam es hin und wieder zu Beschädigungen der Werkzeuge.
DIE COLD JET LÖSUNG
Ziel war es daher, diesen Prozess zu optimieren. Da Stefan Preller bereits Erfahrungen mit der Trockeneisreinigung hatte, kontaktierte er verschiedene Hersteller. Das klassische Verfahren mit Trockeneispellets erwies sich jedoch als nicht geeignet. Denn die reiskorngroßen Eisstücke erzielten bei den feinen Kavitäten und Konturen keine ausreichende Reinigungswirkung, zudem war die Lärmentwicklung viel zu groß. Diese bot das innovative Cold Jet i³ MicroClean System, welches signifikant leiser ist. Bei diesem umweltgerechten Verfahren kommt Kohlendioxid in Form von Eisblöcken zum Einsatz, von denen mit der patentierten “Block-Shaver-Technologie” Partikel abgeschabt werden. Diese bilden im Vergleich zu Pellets einen viel feineren Reinigungsstrahl, der in Verbindung mit speziellen Hochleistungsdüsen für eine schonende und gleichzeitig effektive Behandlung sorgt.
„Das i³ MicroClean Gerät ermöglicht hochsensible, intensive und tiefe Reinigung der Konturen in den Werkzeugen, ohne dass sie dafür ausgebaut werden müssen. Und das sogar bei den extrem feinen Erodierstrukturen der Werkzeuge für die Düsenfertigung“, beschreibt der Industrialisierer.
Für die Reinigung wird das kompakte und mobile Gerät zur jeweiligen Spritzgießmaschine gefahren, an deren Druckluftversorgung angeschlossen, das integrierte Erdungskabel verbunden und das Werkzeug mit der passenden Strahldüse gereinigt. Dafür sind nur noch maximal 45 Minuten erforderlich.
„Durch die enorme Zeiteinsparung konnten wir die Maschinenauslastung bei den Dauerläufern signifikant erhöhen. Dadurch amortisiert sich die Investition in das i3 MicroClean Gerät in weniger als einem Jahr“, freut sich Stefan Preller.
Außerdem hat sich der Personalbedarf für die Reinigung verringert. Einen Beitrag dazu leistet auch die einfache Handhabung des robusten Reinigungssystems.
„Ich habe die Mitarbeiter selbst im Umgang mit der i³ MicroClean geschult und es hat höchstens 20 Minuten gedauert, bis jeder wusste, wie er sicher damit arbeitet“, fügt er hinzu.
Dies brachte einen weiteren Vorteil: War früher speziell geschultes Personal für die Werkzeugreinigung erforderlich, kann sie jetzt von den Maschinenbedienern durchgeführt werden. Dies zahlt sich insbesondere während der Kontischichten am Wochenende aus.
DIE ERGEBNISSE
Auswirkungen hat der Einsatz der i³ MicroClean auch auf die Prozesssicherheit. So ist eine Beschädigung der Werkzeuge praktisch ausgeschlossen.
Die effektive Reinigung gewährleistet außerdem, dass die Entlüftung der Spritzgießwerkzeuge immer optimal ist. Dadurch kommt es bei den Validierungstests der Steckersysteme zu keinen Ausfällen mehr.
„Ich würde sagen, dass wir die Prozesssicherheit bei dieser Produktgruppe durch das Trockeneisschneereinigungssystem um 25 Prozent erhöht haben“, berichtet Stefan Preller.
Gleichzeitig wurden Arbeitssicherheit und Umweltschutz erhöht. Denn der Einsatz von Lösungsmittel konnte deutlich reduziert werden.
Bei A. Raymond in Lörrach sind inzwischen drei i³ MicroClean Systeme von Cold Jet im Einsatz. Zwei davon werden für die alle zwei Tage erforderliche Werkzeugreinigung der rund 20 Maschinen für das Spritzgießen von Dauerläufer-Produkten eingesetzt. Die dritte steht der Abteilung Technische Kunststoff-Wartung für die Reinigung anderer Spritzgießwerkzeuge zur Verfügung.
„Ich bin sicher, dass diese Geräte auch in anderen Werken zum Einsatz kommen. Denn die damit zu erzielenden Einsparungen an Zeit und Kosten sind enorm. Gleichzeitig ermöglichen sie eine signifikante Erhöhung der Prozesssicherheit und unterstützen uns damit dabei, unseren hohen Qualitätsstandard zu halten“, resümiert Stefan Preller.