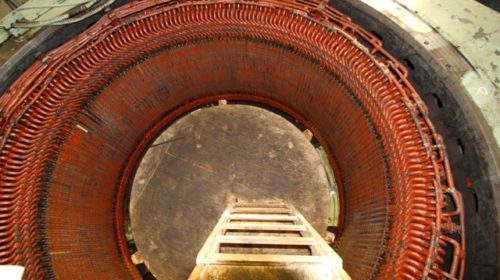
Facility saves 30-40% on energy costs
THE SITUATION
Manufacturers and service providers are feeling the effect of today’s energy expense and price increases. In the vast majority of industries, energy management has no traditional place on the organizational chart, in job descriptions or in performance outcomes. Most decision makers believe the solution to the problem is to find the lowest available energy prices.
Electric motors account for up to 80% of all available electric energy used by an industrial site. They also waste up to 50% of electric energy due to inefficient motor optimization. Some reasons for these inefficiencies include: high ambient temperatures, unbalanced voltage, improper loading, inadequate ventilation, misalignment, vibrations, improper lubrication, defective drive components and most importantly, contamination.
Contamination is a surface coating that causes electric motors to run hotter than normal. By design, electric motors have cooling fans that draw air over the external shell. If not properly cleaned, contamination will build up over time and clog and defect the motor’s ability to cool itself and run at ambient temperature. Hot, contaminated motors running in these conditions increase the amount of energy and thus, increase the cost the motor needs to operate.
“When dirt, soot, grease and oil build up in production facilities over time, machinery can begin to overheat and function improperly, leading to potential failure and creating an unsafe working environment,” said Greg Battle, President and CEO of Motor Techniques, Inc. “A clean electric motor runs cooler and also uses less energy than a dirty one. In order to fully decontaminate an electric motor and increase motor optimization, it must be thoroughly cleaned.”
THE PROBLEM
The most common way to clean electric motors is to take them out of service and clean manually with rags and industrial solvents. To avoid this interruption in production, cleaning is often delayed extensively, which leads to an inefficient motor and/or eventual motor failure. Most of the industrial solvents used have a very low flash point, creating a fire hazard and possible outages. They also emit unhealthy fumes and the manual application of the solvents leaves secondary debris such as lint and cloth on the motor surfaces.
Additional methods of motor cleaning include soda blasting, walnut shell blasting and pressure washing or steam cleaning. Soda and shell blasting can be too abrasive for the motors and require a system shutdown. Pressure washing or steam cleaning the electrical system of a hot, running motor can create a highly dangerous situation. These methods are also time intensive and leave behind debris.
THE SOLUTION
Dry Ice Blasting Technologies (DIBT), a division of Houston-Johnson, Inc. (HJI), is a leading provider of dry ice cleaning services. Motor Techniques, Inc. (MTI) specializes in tracking and monitoring motor performance. Both companies are certified minority business enterprises and bring years of expertise in helping customers realize operational efficiencies while reducing energy costs. DIBT and MTI, in cooperation with each other, established a joint venture company, Conservation Solutions. Conservation Solutions provides methods to locate, analyze and improve performance of industrial electric motor systems, restoring them to peak performance, with minimal disruption to client operations.
Conservation Solutions was the first to recommend Cold Jet dry ice cleaning for motors. They have discovered an overall cost savings – with both electricity usage and man hours – when using dry ice versus alternative methods.
Cold Jet dry ice cleaning provides a quick, safe, non-toxic and economical cleaning solution for facilities, industrial equipment, machinery, machine tools and assembly line equipment. It has met the Electrical Industry’s challenge of operating efficiency and uptime because dry ice cleaning can restore both rotating and stationary electrical equipment to peak performance with dramatically shorter outages.
Dry ice cleaning cleans in-place without major disassembly or cool down and is non-abrasive, non-conductive and non-corrosive. It is a completely dry and clean process as it does not use water. The cleaning media, dry ice, sublimates upon impact, disappearing without adding secondary waste. The only waste is the material being removed. The Cold Jet systems can clean on and around hydraulic power units and electrical power and distribution components and minimize the disposal of hazardous wastes. When pertaining to general maintenance and facilities cleaning, cleaning time can be reduced up to 80% with Cold Jet dry ice cleaning.
“With the flexibility to quickly restore and recondition various sizes and types of industrial equipment and machinery with Cold Jet dry ice cleaning, we minimize the costly downtime and disruption generally associated with industrial cleaning,” said Derek Bland, Vice President of New Business Development for Houston-Johnson, Inc. and DIBT.
THE RESULTS
Conservation Solutions has analyzed multiple projects before and after the use of dry ice cleaning in order to gauge the effectiveness and overall time and cost savings. The cost savings for using dry ice can be figured in Mega-watts and man hours. In order to obtain their results, they used a CSI 510 non-contact infrared scanner gauge that measures the detection of contaminated hot motors. The scanner measures 0-1600 degrees within 99% accuracy. They measure the load (energy required for a particular job) before and after cleaning. A Mega-watt has a standard flat cost to the facility and using less Mega-watts to clean results in a direct savings to the company. The savings are instant and can be calculated as soon as the cleaning is complete and verified by the gauges. Alternative methods are much slower and require excessive man hours for secondary clean up.
SUCCESSFUL SOLUTION FOR AUTOMOTIVE MANUFACTURER
An automotive manufacturer in Michigan had a bank of five 300 horsepower motors, each totaling $100k to run each year. In order to decrease their annual spend, they reached out to Conservation Solutions. After disassembly, two inches of contamination was discovered on each motor that had built up over time and from lack of regular cleaning and maintenance. Cold Jet dry ice cleaning was used to remove the surface contamination and then a putty knife was used to clean the inside of the motor cap surface. The contamination on the inner and outer cap weighed a total of 2.7 lbs. After implementing regular cleaning with dry ice, there was an instant energy savings of 42% for the company.
PROVEN RESULTS FOR INDUSTRIAL DRY CLEANER