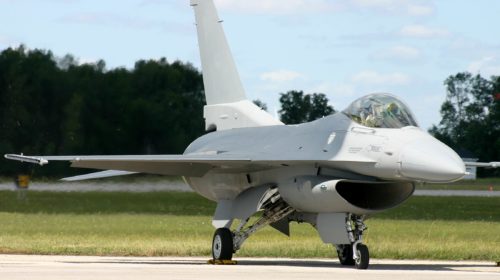
Dry ice blasting removes pitted corrosion for a more effective weld
THE SITUATION
The Little Creek Amphibious Base in Norfolk, Virginia, is the major operating base for the Amphibious Forces in the United States Navy’s Atlantic Fleet. The base is mainly dedicated to amphibious operations, which makes it unique amongst US naval bases. Little Creek’s mission is to provide support and services to operating forces and shore commands. The 61 piers surrounding Little Creek Channel provide docking facilities for approximately 30 Navy ships homeported there. Included in those ships are Landing Craft Air Cushions (LCAC), or more commonly known as hovercrafts. These ships are used by the Navy to transport equipment from a ship to the shore. The base is responsible for maintaining, inspecting and repairing these ships as needed.
THE PROBLEM
The LCACs have aluminum hulls, which can cause issues with corrosion. When the aluminum becomes corroded, it is difficult to repair the hull. When the hull needs to be repaired, a new piece is welded into place, but the corrosion was preventing the naval base from being able to properly weld the pieces together.
“We’re removing the corrosion from the aluminum because the military is having a hard time welding the aluminum back together when they put in a new piece, due to the conductivity,” said Tom Devine, Project Manager, Amee Bay, an engineering and technical services firm that specializes in dry ice cleaning.
The base was searching for a solution that would be able to clean the surface corrosion from the aluminum, but also remove the corrosion that was pitted in the aluminum, which would lower the conductivity levels. The previous method of cleaning was mostly mechanical cleaning, which included wire brushes, solvents and various types of pressure washing. These methods were timely and not as effective as they had hoped in removing the corrosion.
“Power washing is doing nothing but taking the corrosion off, but when it sits, the corrosion comes right back,” said Devine. “It’s not getting the corrosion deep enough down to the metal where the weld can be done where it needs to be done.”
THE SOLUTION
Amee Bay was contacted by the base to demonstrate dry ice cleaning as a potential solution.
Cold Jet’s dry ice cleaning system uses non-abrasive media in the form of recycled CO2 pellets that won’t damage surfaces or equipment. The combination of dry ice cleaning’s kinetic energy and thermal effects break the connection between the dirt and surface, lifting away contaminants. Unlike blasting with other media, dry ice cleaning does not leave any secondary waste, because the dry ice particles sublimate upon impact – converting from solid to gas. Dry ice cleaning is safe and non-toxic, does not create downstream contamination and reduces or eliminates employee exposure to dangerous chemical cleaning agents.
THE RESULTS
Using Cold Jet’s Aero 40 system, the firm demonstrated the process on pieces of aluminum and tested the conductivity levels to determine if the process was removing the deep pitted corrosion.
“The beginning conductivity tests were at 2000; we brought that down to 161,” said Devine. “The other readings we took were at 195; we brought them down to 42. And another one was at 161 and we brought it down to 106. On a scale of 1-10, the corrosion level was at a 10. We brought it down to a 2.”
Dry ice cleaning safely and successfully lowered the conductivity levels and enabled the base to better prepare the surface of the aluminum to be welded.
“We took dry ice and went in and blasted the aluminum to remove the corrosion to lower the conductivity levels so the aluminum is easier to be welded without having to grind it down to where the metal will meet better and weld better,” said Devine.
Cold Jet’s dry ice cleaning process helped save the base time and money. The base no longer had to spend the time to grind the aluminum down or waste money by scrapping pieces of aluminum that they were not able to weld. The cleaning process was also much faster and more effective than the previous manual processes.