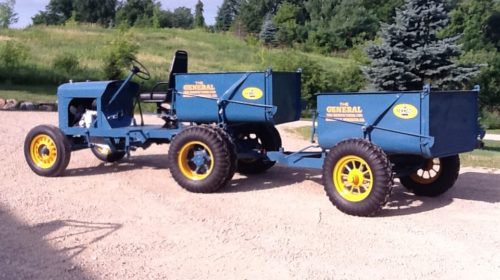
Paint on historic lighthouse removed without creating secondary waste
THE SITUATION
With its dome nearly 800 feet above sea level, the Split Rock Lighthouse is constantly exposed to heavy winds and rain, which over time have damaged the sand colored sentinel. As mother nature continues to take her toll on the property, the Minnesota Historical Society (MHS) faces the constant challenge of trying to keep the landmark clean while preventing further damage to the lighthouse’s exposed and aging surfaces. In the spring of 2008, and in preparation of the lighthouse’s 100th anniversary in 2010, the lighthouse underwent a complete restoration to once again help prepare one of Minnesota’s most well known landmarks for future decades.
THE PROBLEM
While there are many cleaning processes to restore historic lighthouses, most are extensive and costly. In a previous restoration in the early 1990s, MHS hired a company to use soda blasting to prepare the lighthouse for a new coat of paint. Soda blasting uses fine sodium powder, which left residue on the cast iron and on the insides of the lighthouse and inner workings of the rare Fresnel lens components. The soda residue also prevented the new paint from bonding to the lighthouse surfaces. In addition to a new coat of paint, the lighthouse needed a complete cleaning of its cast iron deck and removal of old titanium putty from pits in its cast iron roof. With a focus on a complete restoration and finding a cleaning solution that would not damage the lighthouse or remove any metal, MHS evaluated a number of different cleaning systems and solutions.
THE SOLUTION
“We evaluated a number of cleaning methods, and our analysis found that sand and other forms of media blasting were quite destructive in the restoration of historical property,” said Paul Waugh, Collaborative Design Group Leed AP and project manager for the Split Rock Lighthouse Restoration Project. “Finding a solution that would meet all of our restoration needs was going to be quite a challenge for the project.”
CDG conducted research on the dry ice blast cleaning process and found Cold Jet on the Internet. CDG specifically liked the fact that dry ice blasting promoted itself as a method that can clean electric components and will not harm them. Another major factor was that dry ice blasting produces zero residue, unlike soda blasting, and does not generate any secondary waste.
Veit & Company, a Rogers, Minnesota-based cleaning contractor, was invited to demonstrate Cold Jet’s Aero Series of dry ice blast cleaning systems for CDG and MHS.
Dan Gotz, project manager for Veit & Company said, “We were able to demonstrate that Cold Jet’s systems were the most effective solutions for the project. The goal was only to remove the loose and flaking paint, mold and surface contaminants and putty, and we wanted to do so without damaging the interior or exterior of the lantern room. During our demonstration, what ultimately sold MHS on the process was the fact that we were also able to show that dry ice blast cleaning does not produce secondary waste. Any paint chips and debris that we removed during the blasting process could be cleaned up using a shop vac.”
THE RESULTS
During the first part of April 2008, Veit used Cold Jet’s dry ice blast cleaning systems to remove the paint from the cast iron parts. Dry ice blast cleaning accelerates recycled CO2 in the form of solid dry ice particles through a hose and high-velocity nozzle to remove old paint from the surface of the lighthouse. The combination of the kinetic and thermal gradient effects of dry ice blasting breaks the bond between the surface and the residue, which is blasted away and easily removed. The dry ice particles sublimate upon impact, leaving no other cleaning by-product, and eliminating the added cost and inconvenience of secondary waste treatment and disposal.
The Veit crew also cleaned out the pits in the cast iron dome, which had been filled with titanium putty. The putty is the preferred option for filling the pits because it is able to withstand the rough elements that the lighthouse is constantly exposed to. The putty reacts the same as cast iron in that it will expand when heated and contract when cold. MHS was concerned with the areas that were allowing water to leak through or where there was standing water. With the old putty completely removed by the blasting process, MHS was able to put fresh putty in the pits and prevent the leaks.
Because dry ice blast cleaning is a non-abrasive and non-conductive cleaning method, Veit also used the systems to clean the interior and exterior of the lighthouse’s lantern room. The Split Rock maintenance crew was able to control the pressure of the blast stream, which ensured that no additional damage was done to the landmark. Veit was able to clean around the rare and expensive Fresnal lens, which was covered in soda after the prior preservation project.
The entire blasting process took four days, and with little clean up time, painting crews were able to begin priming and painting right away. While the blast cleaning process was a small part of the overall preservation project, it played a major role in prepping the lighthouse for the rest of the work to be done. With the goal to undo what nature has done to Split Rock for nearly 100 years, CDG and Veit were able to help restore the lighthouse to its 1920s appearance using Cold Jet’s modern-day cleaning technology.
Gotz added, “Dry ice blasting is proving its effectiveness in scores of cleaning applications, and throughout the initial preparation phase of the Split Rock Lighthouse project demonstrated that when it comes to historical restoration projects, it’s a process that must be considered.”